软包电池凭借轻量化、高能量密度及设计灵活性等优势,成为动力电池领域的重要技术路线。其核心工艺涵盖极片制备、电芯组装、封装、注液化成等关键环节,每个步骤均需精密控制以实现电池性能与安全性的平衡。以下从工艺流程、技术难点及创新趋势三方面展开分析。
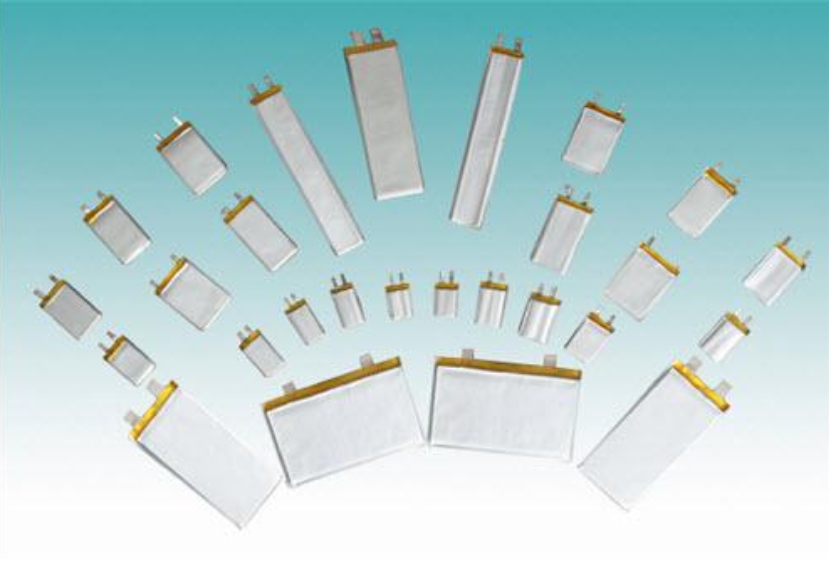
一、核心工艺流程与关键技术
1. 极片制备
极片是电池活性物质的载体,其质量直接影响电池性能:
- 浆料制备与涂布:正负极材料按比例混合形成浆料,通过挤压涂布机均匀涂覆在铝箔(正极)或铜箔(负极)上,随后烘干去除溶剂。涂布精度(面密度偏差≤±1%)和浆料分散性(通过黏度检测控制)是关键。
- 辊压与裁切:涂覆后的极片经辊压机压实以提高面密度(如负极压实密度≥2.0g/cm³),随后通过激光模切机裁切成所需形状。裁切需控制毛刺(≤20μm)和极片对齐度(≤±0.3mm),避免短路风险。
2. 电芯组装
软包电池多采用叠片工艺,与卷绕工艺形成差异化优势:
3. 铝塑膜封装
封装是软包电池工艺的核心,需实现密封性与机械强度的统一:
- 铝塑膜成型(冲坑):根据电芯厚度设计单坑或双坑结构,通过加热模具冲压形成容纳电芯的“Pocket袋”。冲坑深度误差需控制在±0.1mm以内,避免铝塑膜破裂。
- 顶侧封工艺:电芯置入坑槽后,通过热封头(温度180±10℃,压力0.3-0.5MPa)完成顶封与侧封。顶封需借助极耳胶实现金属极耳与PP层的熔合,封装后需检测封印拉力(≥15N/10mm)及厚度均匀性。
- 二次封装(二封):化成后通过真空排气去除气体及多余电解液,再热封气袋区域。此工序需控制真空度(≤-0.09MPa)及封印密封性(氦气泄漏率≤1×1�件)。
4. 注液与化成
- 注液工艺:在干燥房(露点≤-40℃)中注入电解液,注液量精度需达±1%。注液后立即进行预封(一封),防止电解液挥发。
- 化成与整形:首次充电形成SEI膜,过程中会产生气体,需通过夹具挤压使气体进入气袋。高温静置(60℃×24h)后进行真空二封,并修剪气袋完成封装。
二、工艺难点与创新突破
1. 封装工艺的挑战
铝塑膜热封需平衡温度、压力与时间参数。温度过高会导致PP层过度熔化暴露铝层(引发腐蚀),过低则封合强度不足。通过封头平行度校准(误差≤0.05mm)和硅胶垫补偿技术,可提升封装一致性。
2. 极片裁切与叠片效率
传统模具裁切易产生毛刺,采用激光裁切技术(精度±0.1mm)可提升良率。叠片机效率逐步突破,单机产能达0.2PPM(片/分钟),但仍低于卷绕工艺,需通过多工位联动优化效率。
3. 材料与工艺协同创新
三、技术趋势与展望
- 大电芯与叠片工艺结合:孚能科技SPS方案通过增大电芯尺寸(厚度8-20mm)提升系统能量密度(体积利用率75%),搭配卧式叠片技术实现高效成组。
- 智能化与在线检测:引入AI视觉检测极片对齐度,结合X-ray实时监控卷芯平行度,减少人工干预。
- 固态电池前驱体工艺:软包结构适配固态电解质涂层隔膜(如LATP涂层),通过真空热压工艺实现电解质与极片的紧密贴合。
软包电池工艺以高精度封装和叠片技术为核心,需在材料创新(如硅碳负极)、工艺控制(如极片裁切精度)及设备升级(如高速叠片机)多维度突破。未来,随着CTP集成技术和固态电解质的成熟,软包电池有望进一步提升能量密度至350Wh/kg以上,成为电动汽车与储能领域的主流选择。