在现代电子产品制造中,芯片、电池、显示屏等核心组件的性能与可靠性直接关系到产品的质量。而这些精密元器件的生产过程对环境条件要求极为严苛——微小的尘埃、氧气、水分或静电都可能成为致命的缺陷源。手套箱作为一种高度密封、可控环境的工作设备,在电子产品生产中扮演着至关重要的角色,为制造流程提供了“无菌、无氧、无尘”的屏障,确保产品质量、工艺稳定性与生产安全。本文将深入探讨手套箱如何通过多重技术手段保障电子产品生产。
一、隔绝污染:构建超洁净环境的核心屏障
电子产品制造对环境的洁净度要求近乎苛刻。例如,半导体晶圆加工需在百级甚至十级洁净室中进行,任何大于0.1微米的颗粒都可能造成电路短路或缺陷。手套箱通过以下机制实现污染隔绝:
- 高密封性箱体结构:采用不锈钢或特殊合金材质,结合连续焊接与无损检测技术,确保箱体无泄漏。密封胶条、过渡舱双门互锁设计等细节,防止外界空气渗入,形成独立密闭空间。
- 高效气体净化系统:内置多级过滤模块(如HEPA/ULPA过滤器),可过滤掉0.1微米以上的颗粒;配合分子筛吸附水分、钯催化剂除氧,将箱内氧气含量降至0.1ppm以下,露点温度低于-80℃,消除水氧威胁。
- 正压控制:通过持续输入惰性气体(如氮气、氩气),维持箱内正压(50-100Pa),迫使外界污染物无法逆向渗透,同时减少开门操作时的空气交换风险。
二、保护敏感材料与工艺:确保关键环节的稳定性
电子产品中许多材料(如锂金属、钙钛矿、OLED有机层)对水氧极度敏感。手套箱通过以下方式保障材料安全:
- 无氧无水环境:在锂电池生产中,手套箱隔绝氧气避免电解液氧化分解,防止电池充电时热失控;在钙钛矿光伏制备中,杜绝水分与氧气接触,避免材料结晶缺陷,提升光电转换效率。
- 防静电设计:内部采用防静电材料(如导电涂层、静电消除器),避免静电吸附颗粒或直接损伤芯片。手套材质选用低释气、低粉尘的丁基橡胶,确保操作过程中不引入额外污染。
- 工艺集成与自动化:可集成镀膜机、光刻设备、注液系统等,实现材料处理、沉积、封装的全流程闭环操作,减少人工转移导致的暴露风险。例如,在锂电生产线中,手套箱自动完成扫码、注液、封装,提升效率与良率。
三、精准调控与监测:保障生产过程的可靠性
手套箱不仅是“密封容器”,更是智能化的环境控制中心:
- 温湿度与气体成分精密调控:配备传感器实时监测O₂、H₂O浓度,通过PID算法动态调节气体流量与压力,确保环境参数稳定在工艺要求范围内(如±0.1ppm)。
- 可视化与操作便利性:大尺寸观察窗结合LED照明,清晰呈现内部操作细节;柔性手套设计保证操作的灵敏性,支持芯片焊接、引线键合等高精度动作。
- 安全报警与应急系统:当检测到气体泄漏、压力异常或过滤器堵塞时,立即触发声光报警并自动启动应急措施(如切断气体输入、启动备用净化系统),保护人员与设备安全。
四、应对多样化生产需求:定制化与模块化设计
不同电子产品工艺差异巨大,手套箱通过灵活配置满足多样化需求:
- 定制化模块集成:可根据需求加装有机溶剂吸附器(处理腐蚀性材料)、冷却装置(控制材料温度)、显微投影系统(辅助微操作)等,适应半导体光刻、OLED蒸镀等特定工艺。
- 生产线联动能力:在大型工厂中,手套箱可与自动化输送线、检测设备无缝对接,形成从原料处理到成品封装的无污染流水线,减少人为干预,提升产能与一致性。
五、维护与监管:持续保障环境稳定性
为确保手套箱长期有效,严格的运维管理不可或缺:
- 定期检测与校准:每季度对气体净化系统、密封性、传感器进行校准,使用尘埃粒子计数器验证洁净度,确保设备性能不衰减。
- 过滤器更换与清洁:根据使用频率,每3-6个月更换HEPA过滤器,定期清洁箱体内壁与手套接口,避免积累的污染物影响环境。
- 操作规范培训:要求操作人员严格遵循SOP(标准操作流程),包括物品预处理、手套检查、过渡舱净化步骤,降低人为失误带来的风险。
随着电子产品向微型化、高性能化发展(如3nm芯片、固态电池),手套箱的技术迭代将持续加速。智能化方向将引入物联网监测、AI预测维护,进一步降低故障率;模块化设计将支持快速重组,适应快速迭代的工艺需求。作为精密制造的“环境守护者”,手套箱不仅保障了当前电子产品的可靠性,更推动着下一代技术的突破——在追求极致性能的道路上,它始终是工程师最坚实的“隐形助手”。
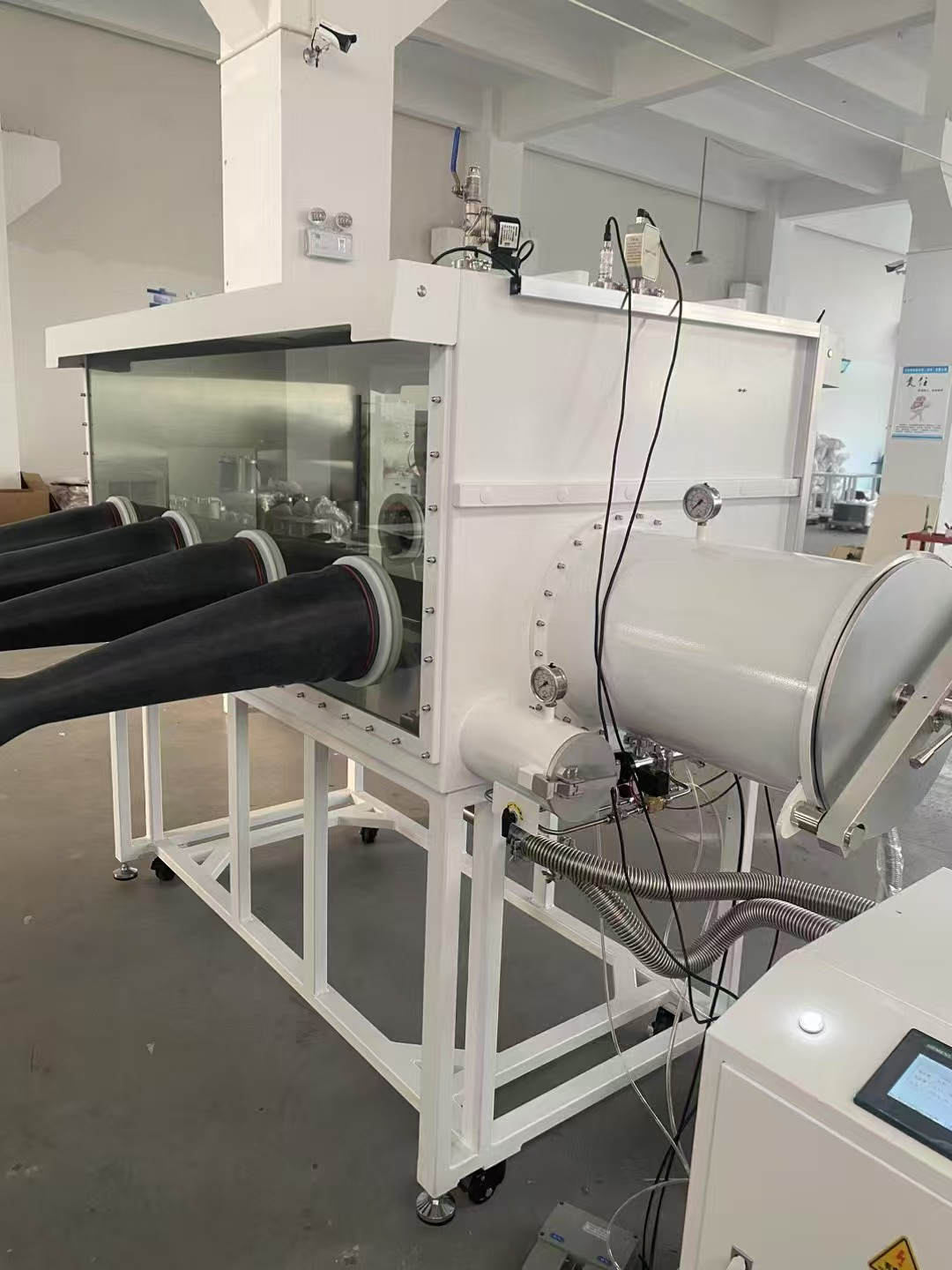